It’s always amazing where 3D printing can be found! In recent weeks, iFactory3D has been increasingly on the road at trade fairs in a wide variety of industries to draw attention to the diverse possibilities of 3D belt printers in numerous business fields. There is no fixed target group for 3D belt printers, everyone can become a producer with a printer from iFactory3D. Whether of prototypes in unlimited length, or to bring the own product or its variations in small runs quickly to the market.
3D belt printing for orthopedic insoles
The small trade fair marathon started already in March, in Kassel at the EXPOLIFE. The important trade fair for medical and orthopedic technology took place from March 16th to 18th. iFactory3D was continuously on site with one employee, later even the CEO joined. This is the result of the experience iFactory3D has gained with its 3D conveyor belt technology in the field of orthopedic shoe insoles. This production area has proven to be extremely suitable for additive series production. All the special features of 3D belt printers can be optimally utilized here: The queuing function for print jobs makes it possible to produce even personalized products in a consistently automated manner. The continious conveyor belt as printing surface means that there are no restrictions on shoe sizes.
Unlike Cartesian printers, the specific printing angle automatically ensures smooth edges and a uniform surface finish. The 45° angle is also responsible for considerable material savings; a 3D conveyor belt printer can largely dispense with printing support structures. This also effectively saves printing and post-processing time. The production of custom inlays with belt printers saves up to 80% of material compared to the usual subtractive process. That’s good for the wallet and the environment.
EXPOLIFE trade fair as launch pad for new belt technology
And as the team had already expected based on previous impressions, the One Pro 3D belt printer was met with an extremely positive response from visitors to the trade show. There, in addition to the already available One Pro, a new printer project was also presented, with which iFactory3D GmbH intends to address the requirements for producing shoe insoles even more specifically. The new generation of 3D conveyor belt printers thus found a great stage at this trade fair.
FIBO offers a wide variety of applications for automated additive manufacturing
Physical health was also the focus at FIBO, but from a different angle. Nevertheless, the One Pro is equally qualified for the production of fitness equipment, equipment prototypes and all kinds of accessories for the fitness sector. Covers and panels, as well as mechanical couplings, can be printed in one piece on site without relying on a huge floor space including an AM industrial machine. For bottle holders, attachments and the like, on the other hand, the serial printing function comes into play again.
Hannover Messe demonstrates breadth of manufacturing industry and opens new cooperation for iFactory3D
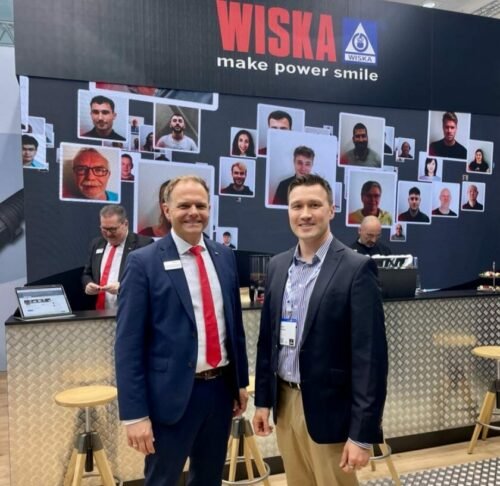
With a product that is the right solution for so many industries when it comes to intermediate quantities between one-offs and mass production, Hannover Messe is the place to be. One of the largest international industrial trade shows once again demonstrated how innovative and progressive the manufacturing industry is. In addition to the lively exchange about the possibilities of the One Pro for respective companies, one encounter, in particular, stood out during this visit to the fair. CEO Artur Steffen met the managing director of WISKA Hoppmann GmbH, who is already an investor in iFactory3D. During the meeting, a strategy was discussed to sustainably integrate 3D printing with conveyor belt into marine construction. The different requirement profiles of the various subsectors within there can only benefit from the flexibility of the all-in-one belt printer. The first joint brainstorming on this idea will be worked out in detail with Ronald Hoppmann in the near future.
Next Stop: Rapid.tech trade fair 2023
And even though the many impressions are piling up, iFactory3D is not tired yet. The next trade fair is already just around the corner. The iFactory3D team will also be present at the Rapid.Tech trade fair in Erfurt. At the event, which is dedicated exclusively to additive manufacturing, the printer manufacturers will feel right at home. Here they expect many inspirations – for possible future products – technical exchange about modifications and improvements, contact cultivation with allies and fellow campaigners. Of course, belt printer customers and prospects are also welcome to personally meet with iFactory3D founders and staff during the show from May 9-11. So, come on by!